GIRI training case study - Bouygues UK hits targets at Welsh school
9 May 23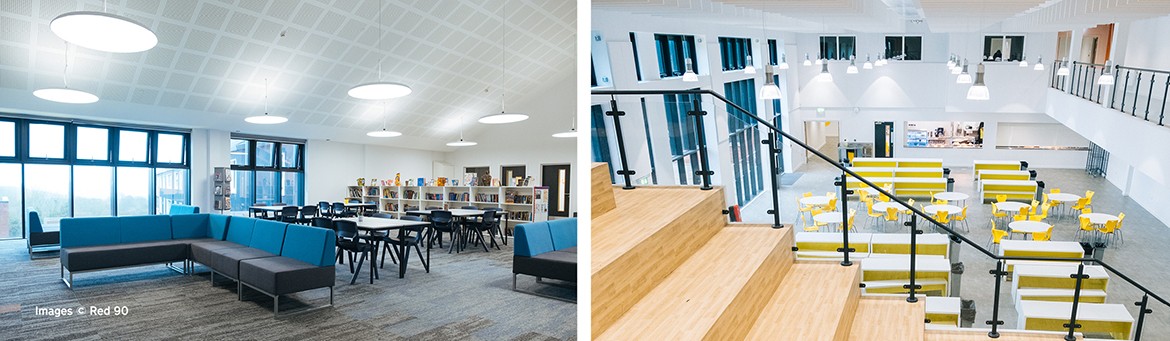
A collaborative approach and the application of key GIRI principles helped Bouygues UK meet the time, cost, and quality targets for the first phase of the Pencoedtre High School project for the Vale of Glamorgan Council.
About the project
The new Pencoedtre High School is part of the Welsh Government’s 21st century schools investment programme. It is located on the grounds of the existing Brynhafren Comprehensive School, and the first phase of work concerned the delivery of a new three-storey school for 1,200 pupils.
Bouygues UK is now working on the second phase, demolishing the old school buildings, and creating additional on-site parking areas plus landscaping and sporting facilities that include an all-weather hockey pitch, grass pitches and a multi-use general activities playing area.
The case for training
GIRI delivered training to 52 delegates involved in the project across six courses: Strategies to eliminate error for leaders of construction projects – parts 1 and 2; Avoiding construction errors at interfaces – part 1: collaboration and part 2: designing for construction; and Reducing errors on construction sites – part 1: supervision skills and part 2: planning skills.
“This training programme focused on delivering against four of our six business objectives: zero defects, 100% projects on time; 100% customer satisfaction; 50% repeat customers,” says Rastislav Blaha, Head of Learning and Development. “We don’t have time or money to waste on poor quality, so this training is intended to embed a quality culture not only across our business, but also our design and supply chain partners.”
A collaborative approach
Collaboration is a central theme in GIRI training. Bouygues UK adopted a collaborative approach with both the client and the supply chain from the start of the project and employed key concepts from GIRI’s training courses to determine strategies and avoid potential issues. “This created a culture where people worked beyond their usual daily responsibilities, forming cross-team cooperation that helped us complete phase one on time,” says Dylan Jones, project lead.
Andrew Lee, regional quality manager, adds that the language used on site has begun to change as a result of the training, with more open questions used in discussions between site management and contractors. “The team strives to collaborate throughout, build positive relationships with the subcontractors and trade operatives, and hold regular planning meetings with trades to discuss and resolve potential issues.”
Build it in your brain
If you can’t visualise what something will look like, you are unlikely to be able to build it without error – that is the theory behind GIRI’s ‘build it in your brain’ concept that is core to the training.
The Bouygues UK team put this concept to good use throughout the project. In one instance, in the early stages of the design of a flue extract for materials-technology equipment, the team set up a collaborative design workshop on site with the flue contractor, MEP contractor, and the façade contractor to find the most efficient route from the equipment to the external wall and discuss the interfaces along the way.
By understanding and discussing the various interfaces, the team was able to find a solution that had the buy-in from all parties.
Press pause to avoid error
Another key message of GIRI’s training is that if you have any doubt about what you are doing, press pause to avoid error. “Throughout the course of the project, the team encountered several instances where the design was reviewed and developed to avoid potential errors,” says Dylan Jones. “This required discussion and collaboration between the production team, consultant designers, supply chain and client.”
Examples of where pressing pause avoided error include a render replacement for an internal courtyard. Discussions with the Bouygues UK post-completion department raised concerns over long-term issues with staining and algae growth. The production team collaborated with the design team, façade contractor and client to instead engineer a cladding solution to eliminate the potential for render problems in this location.
The Get-It-Wrong exercise
The team also ‘pressed pause’ over the choice of screed material. A liquid-anhydrite screed was proposed because it could be laid and trafficked faster, but known previous issues with the anhydrite material prompted the team to carry out a GIRI Get-it-Wrong exercise. This pre-mortem technique is designed to address problems before they occur. In this instance, by drawing on the experiences of a recent Bouygues UK project, the subcontractor, and the expertise of the supplier, a newer product was proposed. The team felt the exercise was a good investment of time to minimise potential risks.
The exercise also highlighted the issue of movement joints. “At first it was thought that none were needed,” says Jason Carter, project manager. “On closer inspection of the material performance characteristic it was agreed that a number of induced joints should be incorporated to actively manage any potential cracking of the screed, with drawings marked up to ensure these were placed as agreed.”
“While this element may appear fairly simple, if it had been missed it would have caused long-term maintenance issues for the new school, causing disruption for the client and difficult additional work for us,” says Jason. “The Get-It-Wrong exercise didn’t just save us time and money, it also had a clear positive impact for the future.”
Images copyright Red 90
